Ben Luly, Product Manager at US press manufacturer Mark Andy, assesses the current market trends and introduces his company’s response to growing demand.
According to market research organisation Future Market Insights, the global market for shrink sleeves is likely to see a CAGR of 6% through 2032. Conference and event company AWA says that the three prime sectors of the current shrink sleeve market are beverages with 53%, food with 23% and household chemicals with 13%. Further, it says that the nutraceutical sector, while small, is growing and that certain sectors are switching from labels to sleeves.
The reasons behind these trends are population growth and sustainability mandates. As part of this, the short run segment is additionally increasing due to demand for versioning to accommodate new products, multiple languages, and promotional designs, as well as security and traceability.
There are many substrate choices for sleeve production, with PVC, PET-G, OPS, PP, PP/PO, PE, and cPET being the most used in the market today. Of these, cPET is interesting because as a newcomer it is more aligned with sustainability issues. When combined with the right ink, it can be separated and recycled.
‘Aimed at the growing mid web space for use with labels, flexible packaging, and light cartons, the Performance Series S9 is ideally suited to shrink sleeve production.’
This chimes well with the current drive to reduce waste and make better use of packaging. Shrink sleeves can be a sustainable solution because they permit more efficient use of the packaging substrate and offer complete coverage of the packaging surface. They can be designed to be recycled with the container or perforated with an indication line to cut and recycle separately. From an aesthetic point of view, sleeves also provide a premium look carrying embellishments across and around the entire product. Usefully, sleeve production also has a low total energy requirement.
New technology
It is with these trends and demands in mind that Mark Andy has observed and responded to customer feedback with a new flexo press, launched at the recent Labelexpo Americas in Chicago. Aimed at the growing mid-web space for use with labels, flexible packaging, and light cartons, the Performance Series S9 is ideally suited to shrink sleeve production.
While many press manufacturers favour the bearer tool design, Mark Andy listened to its customers and came up with a sleeve tool design to match their needs. Based on the well-proven Performance Series P9 flexo platform, the S9 offers a commercially viable alternative for those looking for better operator ergonomics, especially in 22 and 26 inch web widths (560mm and 660mm), and capable of 1000 ft/min (305 m/min).
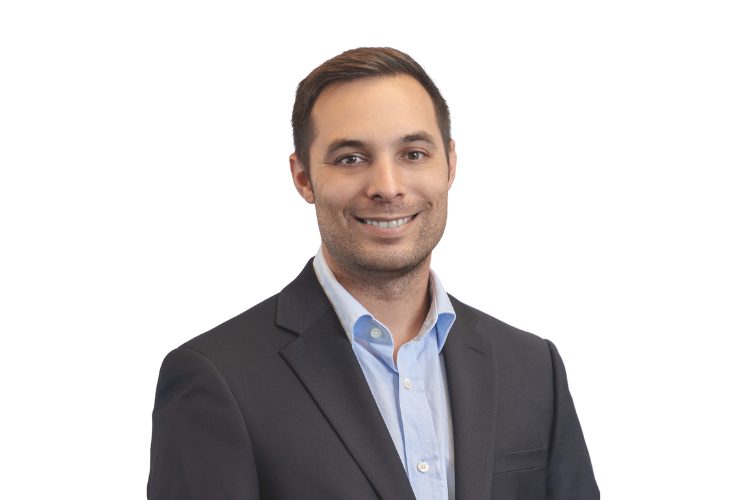
Ben Luly is a Product Manager at Mark Andy
The S9 print station also offers an upward web path creating almost unlimited drying/curing options and capabilities to best suit customers’ individual production requirements. The sleeved tooling allows for a very quick and easy changeover, which balances floorspace with operator needs in today’s often cramped production environments.
Being servo driven also speeds up job changes, and the ink chambers can be ordered with or without pumps to add f lexibility for short and long run lengths. As solvent-based ink is still widely used in flexible packaging, the S9 print station has been designed with this capability in mind. For customers who prefer to use water-based inks, Mark Andy has high performance drying options that are both space and energy efficient.
‘The sleeved tooling allows for a very quick and easy changeover, which balances floorspace with operator needs in today’s often cramped production environments.’
Our unique dryer design allows customers to adjust the recirculation percentage up to 90%, and individually adjust air flow and temperature, or turn the dryer on and off, based on an application’s need. This not only allows for fine tuning of the operational process, but it also reduces energy consumption. The advantages are twofold: increased profitability, and more sustainability, using energy only when needed.
Automation built into the S9 includes the ability to save job profiles and automate registration setup, while reducing waste. A proprietary camera system handles automatic colour to colour registration in both lineal and lateral directions for job setup, while maintaining register at speed.
For converters who need extra embellishments, the S9 can be equipped with cold foil, lamination, or rotary screen units for high build white. It can also be retrofitted with a digital print bar for versioning, with digital inkjet for QR codes, barcodes, or other tracking and traceability features. All these items can be built in a static location, or on an overhead rail for greater flexibility.
Recognising converters’ growing needs for connectivity and data acquisition, Mark Andy offers the latest ProWORX Analytics on the S9. This technology provides data on usage, waste, OEE, and downtime.
In summary
With the foreseen continued growth in shrink sleeve demand, the timing of the launch of the Mark Andy S9 could not be better. It offers key production advantages developed directly from user feedback and raises the bar for sleeve production in the mid web sector. User-friendly and highly automated, it is a production tool designed to meet changing market demand and the shortage of skilled labour in the global converting industry.
Website: https://www.markandy.com/
This article is an advertorial; the featured company created the wording and paid for its placement. It has been checked by Whitmar Publications to ensure that it meets our editorial standards.