Nitrocellulose has long been used in the manufacture of some solvent inks for flexo printing. However, concerns over its compatibility with mechanical recycling processes are seeing alternative ink products launched. The timing could be serendipitous.
With investment in military technology likely set for dramatic increases in many parts of the world, now would be a good time for printers to get out of nitrocellulose (NC).
The highly flammable compound is made using a mixture of nitric acid and sulfuric acid and has historically been used as a propellant in firearms and other explosives. Not for nothing is it also known as guncotton.
This is not really a story about rearmament and world affairs however: it is about recycling of packaging materials, for another use of NC has been in the manufacture of some solvent-based flexo printing inks, where it acts as an effective binder and has properties such as excellent heat-sealing resistance that make it well suited for flexible packaging. Some 70% of ink formulations on the market use NC, according to Sun Chemical.
However, NC has been identified as being an impediment to effective recycling, having limited compatibility with mechanical recycling processes where objects cannot be deinked. The limited thermal stability of NC can lead to unpleasant odour, discolouration, and a lower mechanical strength of the recyclate, which can hinder the material recycling process.
Looming very large on the horizon is legislation such as the EU’s Packaging and Packaging Waste Regulation (PPWR), which mandates that all packaging must be completely recyclable by 2030 and sets targets for recycled content. In response, the ink manufacturing supply chain is increasingly bringing NC-free options to the market for flexo printers.
Recycling compatibility
Flint Group’s VP for technology and product management Paul Winstanley comments: “For the PPWR’s goals to be met, recycling infrastructure must be able to work effectively, and whilst NC-based printing inks are recyclable, NC-free solutions offer improved compatibility with the mechanical recycling process.
“Additionally, under PPWR, producers – including packaging printers – are subject to Extended Producer Responsibility (EPR) schemes, which impose fees based on how easily their packaging materials can be recycled. Therefore, the ink industry is proactively developing new solutions to improve the ability to recycle packaging materials.”
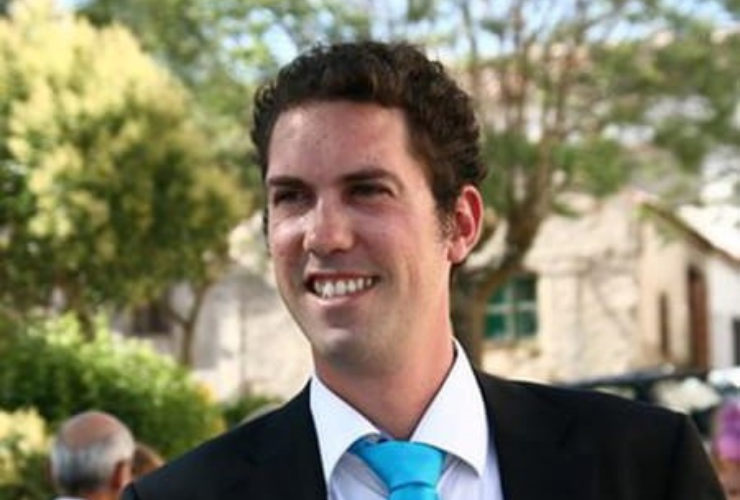
“By adopting these new inks, converters and brand owners can enhance the recyclability of their packaging, avoid potential future taxes, and reduce exposure to the economic risks associated with nitrocellulose.” – Romain Cleret, Sun Chemical
Dr Lars Hancke, manager for business development in flexible packaging at hubergroup Print Solutions, adds to this: “Scientific investigations, including those by RecyClass and Ceflex, indicate that nitrocellulose can pose challenges for mechanical recycling when used at higher concentrations. For instance, RecyClass’ guidelines set a maximum threshold of dry NC binder in PE-based packaging at 0.8% by weight. Ceflex is expected to establish similar thresholds in 2025.”
Germany’s “Minimum Standard” has already declared that NC is incompatible with recycling in PE laminates, and other legislative standards in development all point in a common direction. “We anticipate restrictions on NC-based inks, likely in the form of maximum concentration thresholds,” says Dr Hancke.
Enter NC-free
To address this situation, many ink suppliers are shifting to polyurethane (PU) systems, which offer better compatibility with mechanical recycling. NC-free ink products are consequently starting to become more prominent in the market.
Siegwerk, for example, announced what it claims are the first NC-free surface ink systems for improved recyclability of polyolefin-based packaging in February 2025. These followed hard on the heels of the company’s “NC-free toolbox for flexible packaging”, which includes the company’s full range of colour, white, and overprint varnishes for both lamination and surface applications in gravure and flexo printing. All of these are fully compliant with current recycling guidelines and are available as either ready-to-use ink or a masterbatch system, the company said.
Björn Ewig, head of technology for flexible packaging EMEA at Siegwerk, commented: “With our latest solutions, we have now developed NC-free ink alternatives specifically for surface printing that offer the same technical and mechanical performances as comparable NC-based inks, but with the added benefit of being recyclable.”
Sun Chemical has also been active in developing NC-free solutions, adding new and improved products to its existing product portfolio. This has been a major initiative, the company says, and has leant upon its expertise in polyurethane resin formulation, which it says was strengthened by the acquisition of Sapici in 2022.
Romain Cleret, product director for flexible packaging in EMEA for the company, comments: “Sun Chemical’s laboratories developed new inks for lamination, printable in gravure or flexography. These inks now have printability levels similar to that of NC-based inks, high lamination bond strengths, and lower solvent retention levels. These new formulations extend across the entire lamination market, with a comprehensive range of colours now available.
“In addition, using advanced and proprietary resin formulation, Sun Chemical developed NC-free surface printing inks for polyolefin films and other types of flexible substrates which can achieve the required levels of mechanical resistance without the need for an overprint varnish.”
These inks are particularly well-suited to the automatic bagging market for applications ranging from bakery to frozen foods, the company said, due to properties such mechanical resistance, slip, and resistance to moisture/cold. They are available ready-to-use as well as in dispensing system mode to maintain ink management efficiency.
Seamless transition
From Flint Group comes the PU-based VertixCode NC-free ink for flexo printing, alongside a gravure product (MatrixCode). The company says these solutions are engineered for stability during high-temperature recycling processes, addressing the common issues found with conventional NC based inks and resulting in improved recyclate recovery rates. VertixCode and MatrixCode are designed for optimised colour strength for inks and high opacity for whites, which Flint says ensures consistent quality at high print speeds while also aligning with the evolving regulatory landscape.
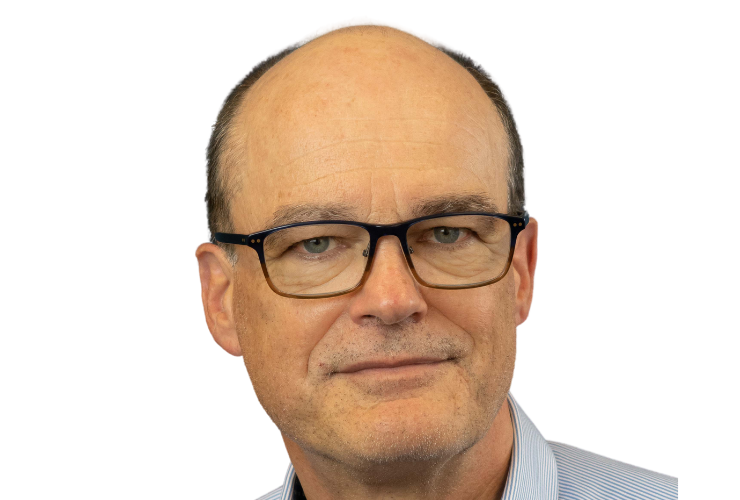
“Scientific investigations indicate that nitrocellulose can pose challenges for mechanical recycling when used at higher
concentrations…we anticipate restrictions on NC-based inks, likely in the form of maximum concentration thresholds.” – Dr Lars Hancke, hubergroup
Eddy Arbogast, senior director for flexible packaging R&D and technology at Flint, said: “We’ve designed our approach to facilitate a seamless transition to NC-free solutions, enabling printers to adapt with minimal disruption and establish themselves as leaders who are focused on a circular economy. Our team is committed to developing high-performance PU based printing inks that not only meet emerging recycling standards but also maintain the reliability of established NC-based solutions.”
Hubergroup’s Gecko Platinum PU inks come into the NC-free discussion, suitable for flexible packaging applications, and providing “high performance” without the disadvantages of NC, according to the company’s Dr Hancke. He adds that if a more minimalist approach is taken, where printers seek to comply with NC thresholds, without switching to completely NC-free solutions, then hubergroup staff will be given an NC calculator, enabling them to answer questions about the compliance of products in accordance with regulatory thresholds with precise information.
Quite understandably, Dr Hancke positions NC-free inks within the wider context of improving the recyclability of printed packaging through a range of measures that can also include adopting mono-material structures and deinking technologies and replacing film with carton alongside barrier solutions.
“For solvent-based inks, nitrocellulose has been a favoured binder for decades due to its excellent properties,” said Dr Hancke. “However, polyurethane based systems like Gecko Platinum are designed to replace nitrocellulose inks in various flexo and gravure printing applications, further supporting the move towards more sustainable packaging solutions. Design for recycling is feasible with the right combination of materials: mono material films, barrier coatings, and printing inks are the key.”
And Sun Chemical’s Romain Cleret outlines in simple terms what benefits there are of flexo printers starting to look at NC-free solvent ink alternatives. He said: “With growing regulatory pressure such as PPWR calling for improved plastic recycling rates, these NC-free solutions provide an opportunity for businesses to stay ahead of legislative changes. By adopting these new inks, converters and brand owners can enhance the recyclability of their packaging, avoid potential future taxes, and reduce exposure to the economic risks associated with nitrocellulose, which is increasingly in demand for other military applications.”