As the industry moves forward, it will be to software, not printing systems, that print businesses will look for enhanced productivity.
When most people think of a printing factory, they imagine the chattering printing presses and finishing lines, the reels of paper or film, the spattered ink barrels; the operator, bent over proof sheets to check colour.
Few think of the software that is ticking along in the background, but it is there, in every facet of the operation, running through the machinery on the production floor and through the office upstairs. Increasingly, it is inter-connecting these different environments, increasingly harnessing Artificial Intelligence, and increasingly sitting up in the cloud, making it accessible from potentially anywhere.
Indeed, it has been much predicted that software, not hardware, will prove to be the biggest differentiator in print efficiency going forward.
This is not likely to be argued against by many, and certainly not the software companies producing systems such as specialised print production workflows; nor, even, would it be disputed by many of the press manufacturers, who are fast becoming accomplished software developers themselves.
‘Taking a broad view of the packaging supply chain, it is clear that greater automation, expanded use of cloud technology, smarter application of artificial intelligence, and stronger integration across fragmented systems are all now key to effective digital transformation,’ says Jan De Roeck, director of industry relations and strategic marketing at Esko. ‘Through collaborating closely with our customers, listening to their concerns and understanding their needs, we are creating innovations that address challenges and supercharge workflow to provide significant measurable advantages in terms of higher productivity and efficiency.’
Workflow landscape
Workflow software such as Esko’s Automation Engine was always intended to enhance print productivity, streamlining processes and addressing almost universal pain points that are still there today: the need to produce more work, faster and without compromising on quality.
There are several ways of viewing the workflow landscape, from individual tools developed for highly specific tasks, up to great platforms of software architecture, the eco systems that all these tools can operate within, and where the big IT trends – cloud computing and AI, for two – make their presence most profoundly felt.
For Esko, that fundamental software architecture has seen a major evolution this year, with the unveiling of its S2 platform, which it describes as a ‘multi-tenant, cloud native platform’. The company says the platform ‘delivers on a new technological reality based on cloud computing, data sharing and artificial intelligence’. All of Esko’s strategic applications, including Automation Engine and the AI-driven Phoenix pre-production software, connect to the new platform, giving users 24/7 real-time access to live data and the same resources, wherever they are in the world.
Flexo printers using Esko applications can integrate these into S2, giving themselves, according to Esko, a ‘quantum leap in connected integrated workflows’. As a result, they will be able to help their brand customers get to market more quickly and efficiently, the company adds. One way this will happen is through the new Job Onboarding, which gives the sales and customer service teams access to the same professional packaging tools as the prepress department.
‘This creates a more streamlined and automated process, speeding up the very start of the supply chain,’ said Mr De Roeck.
On an individual application level, a tool such as Esko Phoenix can also significantly impact productivity. It enables users to fully automate their planning and early estimation processes, replacing formerly time consuming manual steps that were also prone to error. It also includes AI-powered nesting and imposition for sheet-fed and roll-fed print production across flexo and offset applications, helping optimise layouts while reducing waste.
‘Phoenix introduces an innovative method for planning and imposition processes by considering the real world capabilities of printing and finishing equipment on the production floor,’ Mr De Roeck continued. ‘This allows users to perform quicker and more efficient combination planning, minimising press changeovers and setup times. Phoenix empowers our customers to streamline their print workflows, optimise resources, and deliver high-quality, cost-effective production solutions.’
Shifting plates

Dan Pulling of Hybrid Software: ‘As new jobs come into the queue, Tectonics can optimise
the plates and reduce waste.’
Hybrid Software’s main workflow programme is Cloudflow, and underneath its umbrella comes a range of specialised applications. One such is Tectonics – a production tool for automatically optimising flexo plate layout. It therefore seeks to enhance productivity while also bringing with it cost and waste advantages, compared to manual planning of plate layout.
‘Essentially, it’s streamling and automating the process of laying out what needs to be imaged on a plate – whether that’s a separation for a label or a flexible packaging job, or with corrugated, splitting up a separation into different pieces to use less plate material,’ said Dan Pulling, product manager for flexo technologies at Hybrid Software.
Mr Pulling observed that an operator might spend half of their day doing these kinds of plate layout functions manually. ‘With Tectonics, it’s a few minutes. In a typical environment, they will already have prepared some jobs to go to plate. Someone in the morning will take a bunch of jobs and start processing them and they can go ahead and start making some plates. In the meantime, as new jobs come into the queue, Tectonics can continue to optimise the plates and reduce waste. It makes sure everything is ready to run.’
Tectonics is now available in the cloud, and Hybrid says that large multi-site organisations are becomingly increasingly interested in the tool as a single, centralised deployment. The application continues to be developed, with some new features scheduled for a January 2025 release, including the ability to automatically split a printing element that is too large for a single plate into two. This is particularly designed for large-sized corrugated press work.
Cloudflow, the main workflow software from Hybrid, has been cloud-based for a couple of years now and is attracting uptake. Its flexibility is such that Hybrid’s Tom Elton explains that Cloudflow can undertake a role as the leading system within a software environment, dispatching instructions to other systems, or it can act as the following system, taking these instructions from something like an MIS/ERP. A third way is with Cloudflow sitting in the middle, acting as the glue between disparate systems and joining them together. Whichever way it is deployed, the software can ensure data is passed up and downstream, to drive automation and facilitate better decision making.
Enhancing productivity
Bobst is renowned globally for its printing and converting technology, but it increasingly sees itself as a software company too, and it is utilising this capability to deliver enhanced productivity through its heavy metal. The company’s Connect is a cloud-based digital platform that brings together raw machine data to ‘orchestrate’ production, from PDF to the finished product. At the same time, the software integrates with MIS/ERP systems and Manufacturing Execution Systems (MES) to ‘turn production into a single, seamless automated workflow’.
One of its customers is Stora Enso Packaging, which has multiple converting sites across Sweden. Its implementation of Connect has seen a production capacity uplift of 4.4%, a production efficiency increase of 3.3% and machine availability of 98.5%.
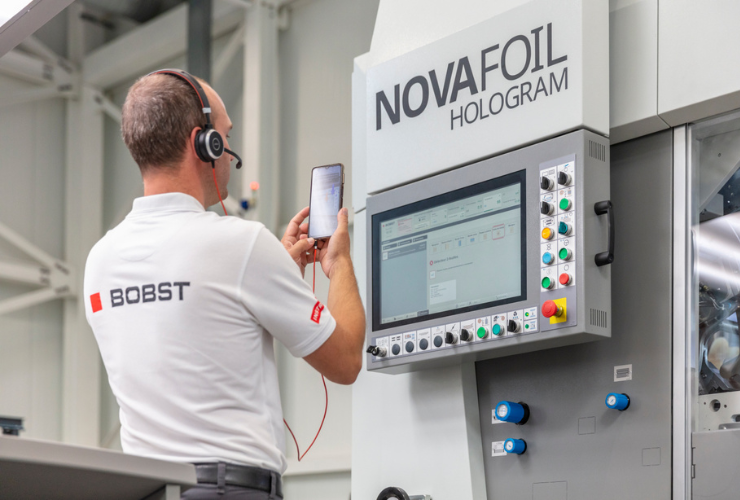
With Bobst systems, Connect brings together raw machine data to ‘orchestrate’ production
‘We’re only just scratching the surface of what is possible when using digital platforms to improve performance and efficiency,’ said Julia Tisserant, marketing communications manager for Services & Performance at Bobst. ‘They open up new frontiers for interconnectivity, automated intelligent decision-making, preventative maintenance, and performance optimisation.’
And Bobst brings us back to the observation made at the start of this article with a final assertion: that with flexo printers and their customers demanding more throughput, more speed, more innovation, it looks increasingly likely that digital platforms, rather than flashy hardware, will be where converters can make the all-important efficiency gains that separate them from the competition.