The right inks with the right substrates and with adherence to high operational and printing standards – there is much to consider when working in the food packaging sector. FlexoTech talks to ink manufacturers about this complex field.
From a printer’s point of view, food packaging is too important to get wrong, and in this context, getting it ‘wrong’ does not mean just a few print quality defects; it means being responsible for parts of the printing process, chiefly inks and substrates, that lead to some kind of negative impact on the food product or its consumer.
It is, of course, for this reason that there are classifications that help to identify the right materials. In the inks sphere, that means ‘food contact’ inks and what used to be called ‘low migration’ but are now more commonly referred to as ‘migration compliant’ inks.
Naturally, you would think that any flexo printer operating in this sector would be entirely conversant with all the issues around producing safe food packaging. In fact, that’s not necessarily the case, according to several ink manufacturers that sell food contact and migration compliant inks to the market.
Mark Heylen, senior director for Narrow Web R&D and Technology at Flint Group, comments, ‘In general, knowledge and understanding of FCM (Food Contact Material) ink systems are growing in the industry. However, there are certain areas where awareness could still improve. One of these areas relates to the different ways in which migration can occur. Although most people probably think of migration solely in terms of materials transferring through a substrate to the reverse side of the print – otherwise known as ‘penetration migration’ – this is not the only risk. Three other forms of migration must also be mitigated.’
He explains that these are: ‘set-off migration’, which occurs when the printed side of a substrate meets the reverse side of another substrate, for example, when the printed substrate is wound on a reel or stacked during logistics and storage; vapour phase migration, occurring when a product is heated, causing compounds in the packaging to become volatile and evaporate, with these airborne particles then able to contact the food; and condensation or extraction of critical ink and coating components during cooking and sterilisation processes, which could also lead to unwanted materials coming into contact with the packed contents.
There are other misunderstandings too, relating to steps in the manufacturing process that are necessary for reducing migration risk. ‘For example,’ Mr Heylen continues, ‘although FCM inks are well understood, the fact that material choices (ie packaging substrates) define whether a product is suitable for food packaging or not may be less clear. This means inks alone cannot always be considered FCM, as this definition only applies when they are used with specific substrates.’
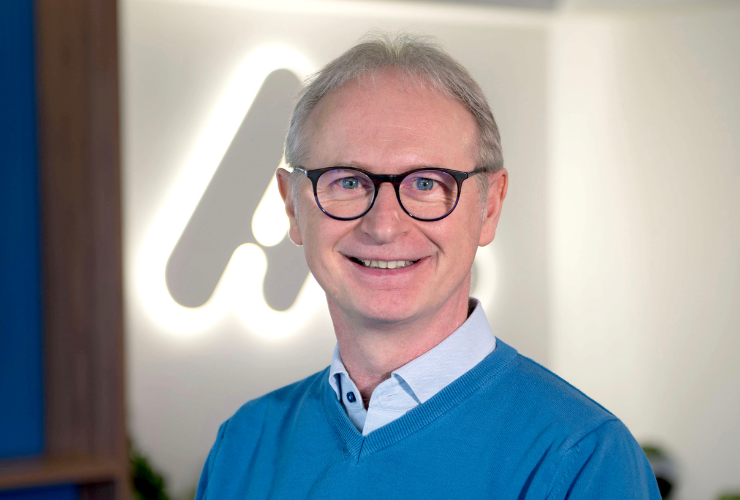
Marc Heylen, Flint Group: ‘Although FCM inks are well understood, the fact that material choices (ie packaging substrates) define whether a product is suitable for food packaging or not may be less clear.’
He also identifies issues such as ensuring inks are dried or cured correctly for the food packaging application and ensuring that changes made to materials over time do not compromise barrier performance, as being further areas where awareness needs improvement. This latter can be almost an accidental process, if care is not taken. For example, a business might decide to change a pack that has been in use for some time, substituting component materials for more cost effective alternatives, without fully considering the reasoning behind their initial inclusion. The question becomes whether due care and consideration has been taken in assessing the barrier properties of the cheaper alternative.
Letter of the law
Other big factors are legislation and compliance responsibility: are printers up to date on evolving legal frameworks and requirements, and is there a clear understanding of where responsibility lies in the critical area of food-safe packaging manufacture. The ink manufacturers themselves bear significant responsibility for ensuring their products remain compliant, and this is a huge ongoing task. But printers also need to be on top of these things. ‘Regulations are ever-changing and new entrants from other market areas such as labels need to pay particular attention to regulations, Good Manufacturing Practice and testing to ensure compliant print is produced,’ says Mark Walkling, product manager for ECP Packaging & Narrow Web Labels at Sun Chemical Europe.
Although his experience is that printing companies and brand owners generally co-operate well to ensure packaging meets the relevant criteria, Resino Inks’ CCO Niels Nielsen says that changes to existing legislation and the introduction of new legislation do provide the potential for problems.
‘The EU Single Use Plastics Directive (SUPD) is a good example,’ he says. ‘It is legislation directed towards reduction of plastics and many designers replace plastics with coated paper and board. This coating, however, is not allowed to be composed of acrylic emulsions, polyurethane emulsions or biodegradable plastics, because they are all chemically modified. The polymers used in SUPD compliant coatings need to be natural polymers which are not chemically modified, and this of course makes formulating high performing barrier coatings more difficult.’
Right responsibility
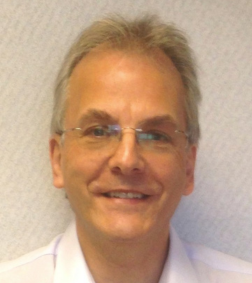
Mark Walkling, Sun Chemical: ‘There are regulations concerning how to test for compliance in different packaging scenarios so it’s important any product or process has been validated to the correct scenario.’
According to Mr Walkling, the biggest area of uncertainty seems to be related to responsibility for ensuring migration compliance of a package. He says, ‘An ink and coating manufacturer can be responsible for providing product that has been fully validated for specific migration scenarios. The final legal responsibility for the product and packaging placed onto the market resides with the food manufacturer/brand owner. There are regulations concerning how to test for compliance in different packaging scenarios so it’s important any product or process has been validated to the correct scenario.’
The issue of responsibility for compliance is also identified by Amanda Jones, business development director at Paragon Inks, who comments, ‘It is the responsibility of the printer/converter to ensure the final packaging meets the required legislation by either using an absolute barrier such as glass or metal, or testing of the final package to demonstrate it meets the requirements.’
She says there is some misunderstanding around this level of responsibility for compliance, adding, ‘Another is that they think we can just produce a certificate to say everything is okay, which is not the case as it is the final packaging that needs testing. Looking at it from a global perspective, there are only a handful of customers who follow the rules properly and conduct regular testing and run the correct products.’
The application needs to be considered in its entirety, considering much more than just the classifications of an ink or a substrate. This begins really at the design and prepress stage and extends into a plethora of factors within the printing factory that could impact on migration or contamination, as well as consideration of processes around the actual packing, storage and consumption of the food itself, such as if the food needs to be heated by the consumer.
‘Printers need to educate themselves on the application,’ explains Jonathan Graunke, VP for UV/EB Technology and assistant R&D director at INX International Ink Co. ‘They need to risk assess the products they are printing, as it is the actual article being regulated, not the ink. Having a robust regulatory team and a robust GMP is a must.’
The potential for contamination is big, he adds. ‘Some of the thresholds of regulation on the ink chemicals are in the parts per billion range. Any contamination from previous jobs or not cleaning turnbars on press, can create a non-compliance situation with the printed article. Even items such as cleaning solvents can be in scope.’
Niels Nielsen of Resino outlines other factors around the application that can impact on food safety, saying, ‘When designing food packaging, it is important to understand the entire package: what is the food type? What is the packaging material? What is the entire process the packaging and food will pass through? What are the storage conditions? During all parts of the process, each step must be considered in relation to food safety.’
Careful consideration
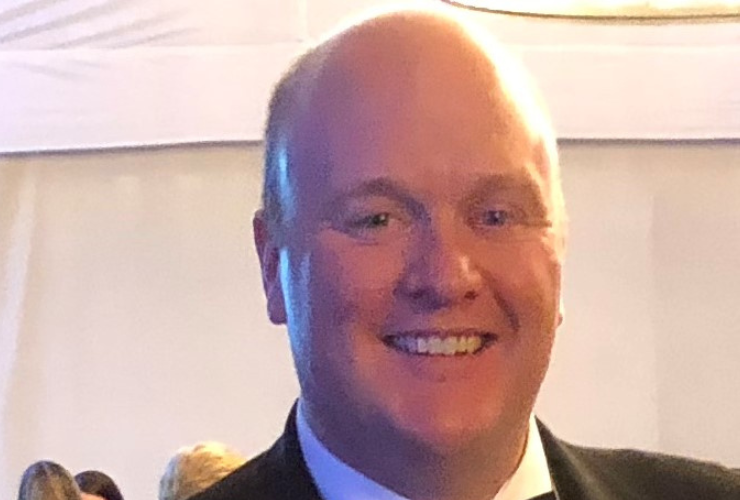
Jonathan Graunke, INX Inks: ‘Printers need to educate themselves on the application. They need to risk assess the products they are printing, as it is the actual article being regulated, not the ink. Having a robust regulatory team and a robust GMP is a must.’
Much of this is outside any sphere of control for the printer of course, but even if the package design and the choice of substrate and ink have all been crafted to minimise the risks of migration or contamination, an unwary printer can still fall foul of food packaging regulations.
Flint Group’s Marc Heylen observes firstly that FCM inks are formulated against defined print conditions provided by equipment manufacturers, including speed and ink densities, and these conditions can change over time, making regularly repeated migration testing vital to ensure ongoing compliance.
He adds, ‘Printers and converters must carefully consider their choice of substrate for barrier performance. Curing equipment must be regularly maintained to ensure lamps are functioning correctly. Good Manufacturing Practices should be followed and, if possible, dedicated presses should be used for low migration inks, as this will help to avoid cross-contamination and reduce downtime in changeovers and cleaning.
‘The storage and handling processes must also be managed to mitigate migration risk. Strong odours in storage areas, and other airborne contaminants like vehicle exhaust fumes, can leach into certain packaging substrates and potentially lead to migration. Set-off migration can also occur during these stages, if substances transfer when stacks of printed material are in contact with each other. Printers must be mindful of unwanted substances ending up on the food contact side. Careful controls are needed to mitigate this risk.’
He is joined in making these observations by Sun Chemical’s Mark Walkling, who told FlexoTech, ‘It’s not just about the inks and coatings, for which the printer needs to obtain specific advice from the supplier, but the materials used on-press such as cleaning solutions and fount solutions (for offset). There must be a risk assessment, not only of products used, but of potential sources of contamination. Examples include using a ‘non-low migration’ product immediately before printing food packaging, cleaning control in mixing stations and dispensers, and insect, rodent and bird control in factories.
‘It’s a big commitment meeting the full requirements for food packaging printing. Process controls to ensure the inks are sufficiently cured or dried every time are essential.’
Legislation is changing the nature of food packaging, and this can have a big impact on the way packs are constructed, and the materials used. A prime example is the beginning of a move away from plastics (propelled in Europe by the EU SUPD) and back towards paper and board, which fundamentally alters barrier considerations. ‘For many years, designers have used a protective layer of plastic on the inside or both the inside and outside of paper and board to protect the food – or protect the paper and board from grease or moisture in the food,’ says Resino Inks’ Niels Nielsen. ‘These plastics now need to be eliminated and this is a challenge to the packaging industry.’
Broad compliance
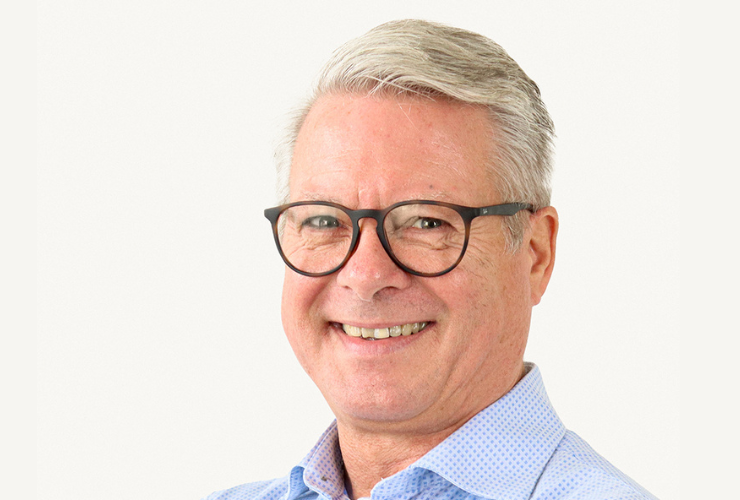
Niels Nielsen, Resino: ‘For many years, designers have used a protective layer of plastic on the inside or both the inside and outside of paper and board to protect the food. These plastics now need to be eliminated, and this is a challenge to the packaging industry.’
There is a complex web of requirements around the printing of food packaging, with the overarching objective being to ensure that materials used in the printing process do not transfer to the packaged food in ways that could affect its taste, smell, safety, substance, and quality. Navigating this complex field successfully is further complicated by the state of flux around regulations, legislation and national or regional boundaries. It is therefore worth emphasising again how important it is for printers to be abreast of relevant regulations and legislation, and that opting for the broadest possible compliance could be instrumental to success for packaging used across multiple geographical markets.
There is currently no standardised regulatory landscape governing the composition of food packaging inks. However, many brands and supply chains have adopted the Swiss Printing Ink Ordinance as their point of reference, due to its comprehensive list of approved materials for use in non-direct contact surfaces of food packaging. The European Printing Ink Association (EuPIA) has also published a Guideline on Printing Inks for use with non-food contact surfaces in food packaging, which certain ink manufacturers have signed up to.
According to Flint Group’s Marc Heylen, however, more changes are afoot in Europe, at least. He says, ‘In January 2026, the German Printing Inks Ordinance will also come into full effect, introducing provisions for certain FCM inks and varnishes used in Germany. The Ordinance will contain a list of permitted substances for use in inks and varnishes, and specific migration limits outlining the amount of a substance that can migrate from the packaging. This differs from Swiss Ordinance in that it covers direct and foreseeable contact, as well as indirect food contact, and looks set to become a common reference point for brands and their printers operating in multiple countries.’