Wide web CI presses are among the biggest beasts prowling the flexo world, but as Sean Smyth writes, they are highly sophisticated pieces of technology too.
CI wide web press technology is a mature part of the flexo industry. Windmöller and Hölscher (W&H) claims to have invented the CI format, and it offers a range of presses, from the new entry level Alphaflex and standard Miraflex, to high performance Novoflex and automated Vistaflex with a full robotic option. Like most press manufacturers, W&H is focused on productivity, efficiency and interconnectivity in production. It calls it Packaging 4.0, with automatic changeovers and consistent printing up to 800m/min at widths up to 2200mm.
Spanish press manufacturer Comexi launched the F1 Evolution at drupa, claimed to be the most automated press at the show. It has an automatic setup system, using Comexi’s Genius Print and Positioning System. There is an optional robotic sleeve and anilox change system, then the Genius Print supports operators across make-readies with a single touch to start the series of changeover actions
automatically. Carles Rodríguez, printing director at Comexi, comments, ‘The new F1 Evolution culminates the renewal of Comexi’s CI flexo range with a multitude of innovations aimed at addressing the challenges faced by our customers. The Genius Board automatically calculates the most efficient way to carry out a job change, guiding operators step by step, and the Genius Run HD system makes bouncing and barring things of the past at 600m/min in the most demanding jobs.’
Wide web machines are used to print corrugated liner, flexible packaging and, interestingly, cartons, as well as non-wovens, wrapping paper and tissues beyond the packaging space. As well as CI there are also unit presses, more commonly used with heavier substrates for cartons, sleeves, cups and also lottery tickets. In the US, CI presses are also used for cartons. Huhtamaki, for example, has ordered
several PCMC presses over the years. ‘They use them for lots of cartons, but particularly important is food service,’ says Michael Ring, VP for print, bag and mail at PCMC parent company, BW Papersystems in Green Bay. ‘We see three solid points for our webfed CI versus sheetfed: you can nest shapes and eliminate a ton of waste; the CI delivers great register for high volume printing at 2000ft/min and the outboard print unit offers the ability to add value-added features on front or backside, varnishes and barrier coatings or coupons on the inside of
food service boxes.’
It is extremely impressive to watch PCMC’s 59-inch-wide beast of a machine starting up and accelerating to 600m/min is a few seconds.
Czech supplier Soma is also adding outboard print on its CI presses for flexibles. The Intelligent Printing Unit (IPU) is an outboard print system added to the Optima CI press, to apply barrier coatings, heat/ cold seal, or functional coatings. It is designed to boost efficiency as a single-pass operation, rather than needing a separate pass which can be avoided as more mono materials are used. The IPU can be configured either upstream or downstream to the printing press with one or two flexo printing decks. The 90° Flexo IPU is the most common because it uses less floorspace.
Carton units
CI carton presses are not the norm in Europe, where unit presses dominate. Danish manufacturer Tresu has long supplied wide web unit presses to Tetra Pak to print reels for drinks cartons. Jumbo rolls will have multi lanes, and these are creased and slit for customers using a Tetra Pak filling line that forms and seals the gable end cartons. The Heidelberg BoardMaster offers zero make-ready for high volume carton applications. The user specifies a press with spare units and, while one job is running, sets up the next on non-printing units using offline 3D plate scanning to pre set the press automatically. When the job is complete, they simply take the print units off impression, switching to
the other units and swapping out the sleeves while the next job is running. This promises zero make-ready and job changeover at 600m/min.
The smaller footprint of CI machines over unit presses is usually an advantage, with models from 1000 to 1800mm wide commonly used in Europe and America. Wide web is less common in Asia, where medium and narrow web still dominate, but that is starting to change as Western manufacturers sell systems there.
Bobst has a range of CI presses in the Vision, Master and Expert models. New presses feature the autonomous smartGPS start-up, with registration and impression set off-line to allow very low substrate waste at change over. This is designed to reduce machine downtime and costs when producing short runs. It helps extend the life of HD plates by printing the real format, avoiding any distortion of dots. This helps consistency, important for adopting standardised extended colour gamut printing. At drupa, Bobst announced the acquisition of Co-ëfficiënt, a Belgian consulting company that includes ECG colour management in its suite of tools to boost efficiency and OEE of print machines.
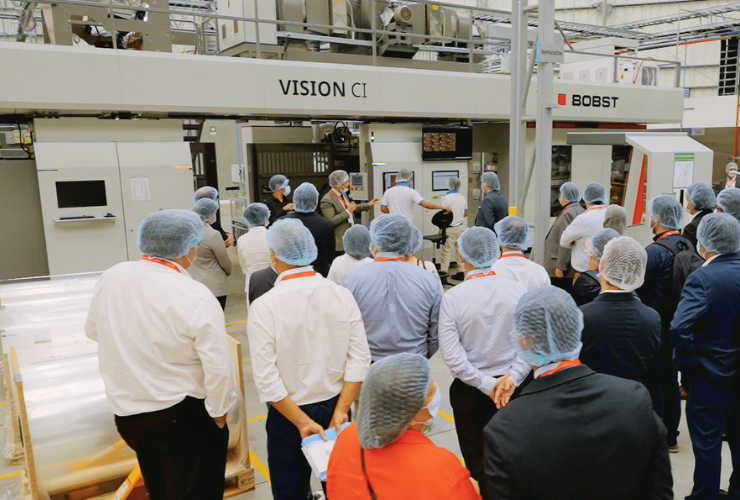
Customers around the Bobst Vision CI press at Litoplas in Guatemala
Bobst is pushing oneECG. Colombian converter Litoplas uses three Bobst presses in a streamlined and optimised ECG workflow. Litoplas employs 500 people, with an annual capacity of 420 million square metres in food, confectionery, and snack segments. It has used ECG printing since 2014, and in 2023 it set up a new facility in Guatemala, with a Vision CI machine using oneECG and a laminator. Antonio Mora, chief customer officer at Litoplas, comments, ‘Configuring our Bobst presses with ECG has revolutionised our printing operations. This allows us to rely less on spot colours, streamline the process and reduce waste, ensuring better outcomes and a much more efficient workflow. We have observed significant improvements in both efficiency and image quality. This has led to consistent, predictable production results, simplified job repeatability, and overall greater productivity.’
Water surge
While solvent inks dominate CI flexible packaging, there is a shift toward water based, and for functional coatings. At high speeds, drying is critical, and while water-based inks do not release VOCs (volatile organic compounds), the energy needed to drive out water when printing non-absorbent films is higher than for solvent. While it is not straightforward to change from solvent to water-based ink, it is a more sustainable approach.
Koenig & Bauer (K&B) offered dual ink systems on machines in 2016, and the XD Pro CI launched in 2023 with a speed of 500m/min when running either solvent or water-based inks in eight or ten colours. It is available in widths from 1000 to 1400mm and repeats from 330 to 850mm. Downstream units can provide coating, laminating or patterned lacquering in a single pass. Christoph Müller, then CEO of K&B Digital and Webfed, commented, ‘With the trend towards packaging recyclability gathering speed, the focus is on the design and production of the original package in a more sustainable way, with thinner and more easily recyclable materials. The XD Pro further expands our portfolio in f lexible packaging. We believe it will become the product of choice to overcome many of the market challenges. We are confident of having significant sales successes.’
The press has high levels of automation and K&B offers PressSupport24, with online diagnosis and telephone support, 24/7. K&B claims it can solve 80% of customer enquiries remotely, avoiding site visits. It provides augmented reality data glasses enabling remote maintenance to see what the customer can see on site though a secure VPN connection. It can then provide step by step instructions to rectify the issue.