While automation has been a key driving factor in the development of plate mounting systems, it is not necessarily the be-all and end-all of what operators need.
The direction of travel with the development of plate mounting systems has been somewhat relentless: increasing automation at every stage where it can be applied to the process.
While this trend is both natural and welcome in the never-ending quest for more efficiency in printing and prepress operations, it has not been without its tensions, according to Mike Attard, managing director of Eurograv, which is a reseller for the Camis plate mounting systems.
‘Flexo printers are viewing the prepress area with much more scrutiny, these past 12 to 18 months,’ he told FlexoTech. ‘Recent investments in complicated and multifaceted robotised mounting systems are not yielding the results expected and printers are only now wondering how they made the massive jump from simple analogue dot spotters to service and calibration intensive automatic systems.’
According to Mr Attard, printers need to remember that they are dealing with ‘delicate and flexible materials’ in both the plate and the mounting tape. He continued, ‘Systems employed to mount these products must be able to mount all plates and all tapes quickly and efficiently, with all subsequent mounted sleeves ‘Press Ready’. Having to reload a sleeve to correct an error from an automatic machine is neither good, nor welcomed.’
He emphasises that the escalating costs of downtime on a flexo press will rapidly erode any margin that the printer might hope to make. ‘Prepress departments must have the right combination of systems to ensure that these failures are very rare occurrences,’ Mr Attard added.
Reliability is key
Reliability of both the machine and the process is key, and factors such as practicality and operational ergonomics feed into this. Camis’s SleeveMaster Auto (SMA) is, as its name suggests, an automatic plate mounting machine, and it was designed to be user friendly, and to offer greater mounting efficiencies than its predecessor, the Camis Irisleeve HD, doing so reliably and repetitively.
‘One of the SMA’s most interesting features is its ability to mount all plates, even those an automatic recognition system can’t detect accurately enough, which is usually due to old and damaged register marks or curled plates. The SMA has an anti-curl system that allows the use of all but the very worst plates, laying them flat on the plate mounting table and registering the dots on the flat via the Double Decker Camera system, which affords even tighter registration tolerances. If the system cannot detect the register marks, due to damage, the operator can position these via push button or indeed like a conventional mounter, so that the presses are always running.’
Mr Attard says that this capability is coupled with a newly improved Taper Slide 3.0 tape applicator on the SMA, to reduce sleeve mounting times by nearly 40% when compared with the Camis Irisleeve HD. The Tape Slide 3.0 mounts both narrow and wide rolls of tape, and can also mount tape crossways, allowing wider then 1380mm sleeves to have perfectly applied tape. It also provides a tape cutting system that doesn’t scratch the sleeve and has a turret for different widths or densities of tapes, which he says enables ‘master flexographers’ to take advantage of using different densities within the same print run.
Part of the process
The evolution of plate mounting systems has been about more than increasing levels of automation, however. Plate mounting is only one part of the entire process, with other steps including cutting tape or plate, demounting, plate cleaning, and QA systems.
‘Over the years, many plate mounters have had an evolution of options like plate support tables, plate cutters or double-sided tape applicators, and pressure rollers to eliminate bubbles between plate and tape or between tape and sleeve/ cylinder, which has improved the workflow in the mounting process, helping the operator considerably,’ said Nick Vindel, international sales manager at Heaford.
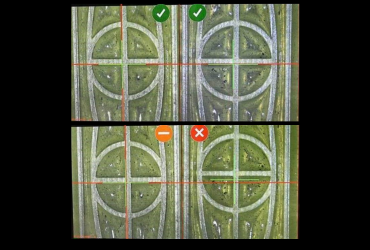
Accuracy checking systems are built in to most plate mounters these days – these examples from Heaford
Many mounters now have inbuilt mounting accuracy checking systems, and even if they do not have this built in, it can often be retrofitted. These image recognition systems confirm the accuracy of the plate mounting and provide a simple visual traffic light system to notify the operator when the register mark is in position.
‘The mount tolerance window is adjustable and can be set during installation or via the password protected engineering page on the machine’s touch screen,’ said Mr Vindel. ‘Crucially, this ensures that every operator works to the same degree of positional accuracy when mounting plates.’
He adds that data input into mounting machines has also changed considerably from older manual machines, with most motorised camera systems now being able to hold a huge database of jobs with mounting coordinates and information, which can prove to be highly useful for repeat or similar jobs. Connections to prepress or art departments can be made, either via established suppliers such as Esko Platepatcher or with networked systems and QR code scanners.
‘These systems allow for the job information to be printed on a job card by the art/prepress department with a QR code which the operator then scans with a QR code scanner on the mounter, automatically populating the mounter with the job information. This increases not just productivity due to time savings, but also reduces human error as there is no need to reinput the information into the mounter.’
Consistent quality
Both plate and sleeve quality are critical within the flexo printing process, if consistent high quality print results are to be achieved. Damage or wear to the sleeves can result in round, high or low dots that affect the quality of the print. Many motorised plate mounters now include scanning systems for checking over the entire surface of the sleeve, including laser scanners, TIR (Total Indicator Runout) contact scanners, and laser TIR for those working with reusable sleeves (ie Twinlock or Polymount), where no mounting tape is required.
‘Heaford’s sleeve scanning options are precision scanning systems for checking, recording and tracking TIR of sleeves and surface quality,’ said Mr Vindel. ‘The advantage of scanning sleeves is that this provides important control over print quality. A regular scanning programme means that damaged or out of specification sleeves do not enter the production process, helping to maximise production efficiency. The tracking system is a predictive maintenance tool that allows the life of a sleeve to be predicted so that it can be replaced before it goes out of specification. In addition, these inspection systems can be used as quality control of the sleeve supplier.’
AV Flexologic also features TIR scanning systems within its range of supporting equipment, including its TIR with Zumbach laser system (called Sleeve Quality Inspection System, SQIS), which scans the entire 3D landscape of self-adhesive sleeves with a claimed accuracy of one micron. This machine can scan and create a report on the condition of tesa Twinlock or Polymount sleeves.
Sleeve preparation is another important part of the process, and sleeve preparation units for plate demounting and tape application deliver a double benefit of removing this step from the plate mounter, reducing bottlenecks, and allowing for tape application and plate removal in a safe and controlled manner. A great deal of waste and cost can be avoided by utilising such systems to eliminate plate damage and wear and to reduce tape usage, so the return on investment on these machines is, according to Nick Vindel of Heaford, relatively easy to calculate. ‘Customers can get payback on their investment in under a year,’ he said.