The anilox roller is a key component of the flexo printing process and, as such, printers need to pay it close scrutiny to make sure that it is in optimum condition and ready to produce quality print. By Charlie Kortens
The anilox roller might, at first glance, seem a relatively simple product performing a relatively simple function, but it is vital that printers inspect it regularly in order to guarantee the standard of their work.
There are a number of different companies able to help you when it comes to anilox inspections, and FlexoTech spoke to several of them in order to gauge how often audits should be carried out, what sort of problems you should be looking out for, how they can be rectified and more.
Pamarco
‘The anilox roll surface contains millions of cells designed for carrying ink from plate to substrate, yet it is very reliable when handled properly,’ says Pamarco’s marketing manager, Shon Cornwell. ‘A well-rounded anilox care programme can provide you with an impressive degree of confidence and stability.
‘Think of anilox inspection and care like running a race: you’ll be able to set a steady, efficient pace if you avoid hurdles like damage, corrosion, and abrasion. Although these obstacles present in a variety of ways, the most common are ink waste, loss of volume, and inconsistency. How can we avoid these problems? One of the best ways is a preventative pressroom audit. These can be completed as part of your regular maintenance schedule, or they can be carried out individually to assist you in identifying specific problems.
‘Every audit consists of the same things, an impression of your anilox cell which is sent off to the lab for a microscopic look at the volume and damage of your current cell structure. Our process starts with our impressions, but we look at your current engraving and the performance of your anilox and make our suggestions to increase quality, performance, and consistency from job to job. In most environments we can make suggestions for new types of engravings that would reduce the need for rework and increase your printing capabilities with an overall look at your pressroom needs. We then look at your cleaning process, checking what kind of chemicals and tools are being used to get rid of the ink and restore volume back to the cell. We also verify if you are properly using doctor blades for smooth application with the right angle of installation, reducing the damage done to the ceramic finish of your anilox roll.
‘Lastly, technological advances such as enhanced cell geometry, improved consistency of engravings, methods of stabilising pH and viscosity, and new techniques for cleaning, combined with the information from an audit, provide you with the ability to prolong the life of your investment with consistent maintenance.’
Cheshire
Sonia Arcos from Cheshire Anilox Technology insists preventative maintenance is key. ‘This means not only ensuring rolls are thoroughly cleaned after each use but also tracking their essential data points,’ she says. ‘For example, before a job even starts, converters need to know if their anilox rolls meet the criteria they logged the last time that job was successfully produced. This includes measuring the volume of the anilox roll using equipment like a Capatch strips, ink drawdown tests, high-power microscopes or interferometric cameras.
‘It is imperative that when an anilox roll is returned to storage that any chips or scoring lines have been documented. The volume should be measured, and the data should be captured so the prepress department knows that roll is ready to run the next job.’
In terms of auditing, Ms Arcos explains, ‘The rollers will be inspected with a high-powered digital microscope for screen parameters, cleanliness, wear, damage and any other aspect that can affect their performance. However, since suppliers are not typically in a printer’s facility on a daily basis, printers should invest in measurement tools and knowledge in order to diagnose and address issues themselves.
‘A well-lit area where the anilox roll is supported by precision bearing blocks is all that is needed to inspect the engraved surface visually. After visual evaluation, the next logical step is to inspect the engraved surface more closely with the assistance of a magnifying device. You need to be able to inspect the engraved surface close enough to determine if the surface is plugged, worn, or damaged.’
Ms Arcos stresses that, ‘cell volume is the primary controlling factor in flexographic printing,’ and, as such, recommends that anilox rolls need to be standardised for each print application to ensure consistency.
programmed refurbishment/renewal, as the data from the measurements can be tracked, so when the anilox is no longer capable of delivering the correct ink volume it can be replaced, this can be caused by poor cleaning, wear and surface damage and it is important, not to just replace the anilox, but to investigate and cure the cause.
She explains, ‘When optimised for various elements required of the printer, including solid coverage, line work, screens, process work, and combinations, the anilox roll’s performance is standardised to reproduce line colours, solid ink density targets, and acceptable dot gain values.’
‘We recommend that a minimum of monthly measurements will allow the printer to track the wear and cleanliness of their anilox, before the problem requires a job to be stopped for remedial action.’
She concludes, ‘Implementing a maintenance and inspection process will save the converter lots of money and time in anilox roll purchases, long set-up times, wasted press time, wasted ink, wasted stock, and lost business.
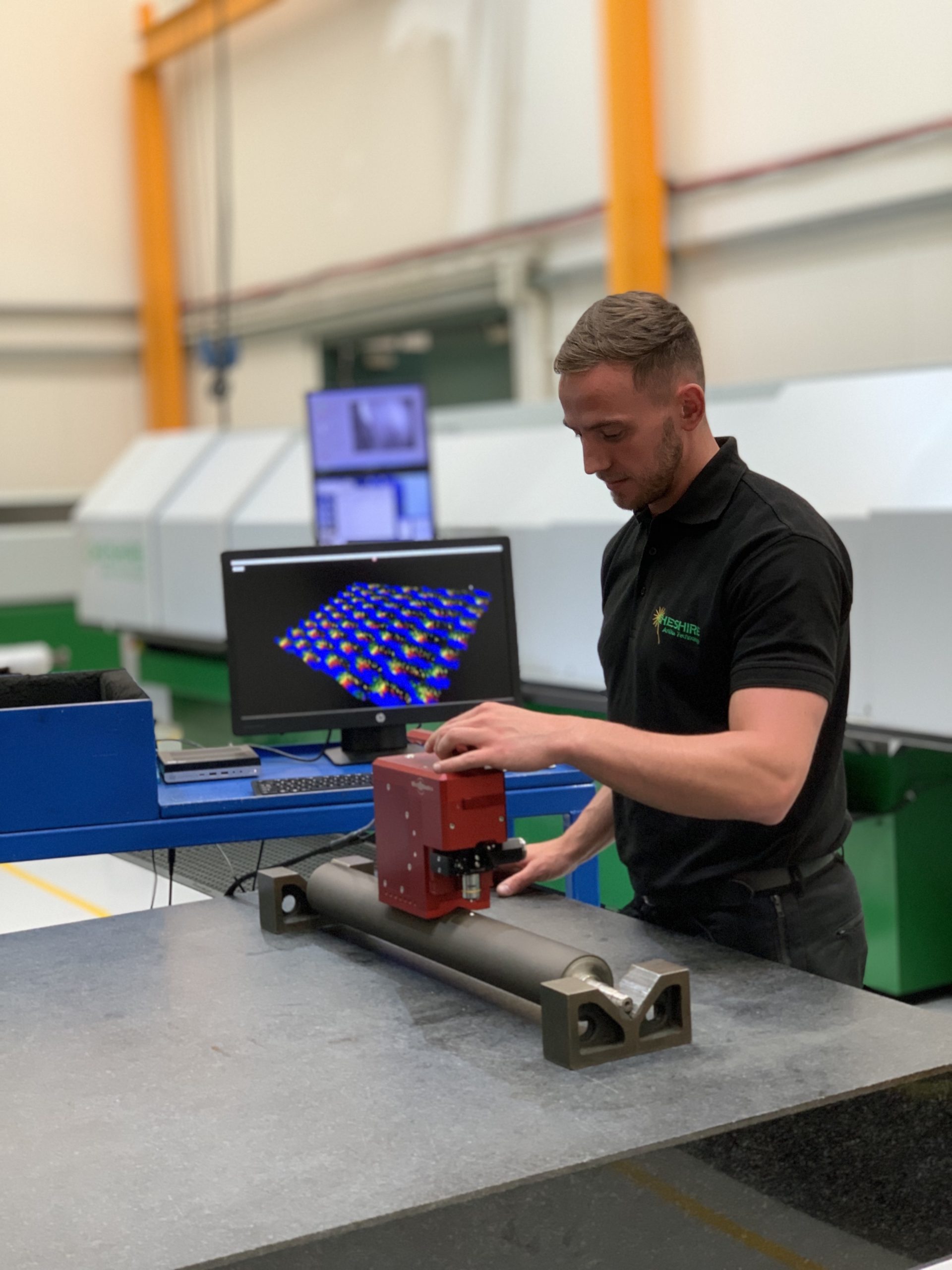
Cell volume is the primary controlling factor in flexographic printing according to Cheshire Anilox Technology
Troika
Troika’s Sarah Wandsworth says that, ‘If you don’t measure your anilox and cleaning effectiveness then you cannot control the print process, causing unnecessary press down time and make-ready waste.’
In terms of how often audits should be carried out, she explains, ‘A simple wipe down between jobs is not sufficient and anilox rolls need a regular full clean to remain efficient, electronic microscopes can show the depth variation, condition of the cells and allow the printer to adjust their cleaning regime and doctor blade settings to prolong the life of their anilox.
‘Taking a proactive approach with your anilox inventory allows for programmed refurbishment/renewal, as the data from the measurements can be tracked, so when the anilox is no longer capable of delivering the correct ink volume it can be replaced, this can be caused by poor cleaning, wear and surface damage and it is important, not to just replace the anilox, but to investigate and cure the cause.
‘We recommend that a minimum of monthly measurements will allow the printer to track the wear and cleanliness of their anilox, before the problem requires a job to be stopped for remedial action.’
When it comes to the actual audit process itself, Ms Wandsworth concludes, ‘Troika developed the AniCAM scanning microscope to allow precise measurement and analysis of anilox and this differs from traditional methods, as the user’s influence over the analysis is removed, allowing accurate, predictable measurements, with the added bonuses of capturing images of cells for ceramic condition and cleaning analysis and a database to show the tracking of wear over time. This allows the printer to predict the refurbishment of worn rollers and make sure their cleaning practices are suitable and providing the right result, having seen the results from many solutions, not all are suitable or providing the quality of cleaning required. Knowing that the new/ refurbished roller meets the printer’s specification allows the printer to be assured of quality of supply.’
ALT
Ade Morton, sales director at ALT, believes that ‘the anilox roller or anilox sleeve is the very heart of the flexographic printing process. It is therefore of great importance that the printer has some method of looking at a high-powered level at the condition of the anilox roller or anilox sleeve.’
He says that implementing a ‘track and trace’ auditing system will allow printers to identify five key issues: contamination, surface damage, score lines, chipping and staining. ‘The above issues will all cause print defects, often resulting in re-work or product rejection, as we are working with a very controlled surface and in micron depths any imperfections can be seen clearly, a very small slight surface scuff could damage hundreds of cells.’
As a result, he says, ‘anilox rollers should be checked over after every print run, this is easily done at the cleaning stage as the operator is in close contact and visually observing the anilox and looking for any changes.’
In terms of a full audit, Mr Morton suggests that this needs to be done at least annually. He explains, ‘A yearly audit of the anilox inventory is essential. The audit can be done in many ways, on press with controlled pulls on a controlled ink and controlled flexo head set up and colour readings, with high powered inspection equipment, or with a draw down system.
‘New developments in engraving technology are helping us to reduce the impacts of some of the issues we see, here at ALT we are seeing more of our elongated technology being utilised as this can help with cells evacuating ink and coating better and running cleaner, this can help in reducing the cleaning cycles. The elongated technology can help to reduce scoring issues as foreign particles are allowed to move freer under the doctor blade and in the cell, thus reducing the possibility of particles lodging behind the doctor blade and scoring the anilox roll.
‘Whatever method of anilox inventory control is selected, the key is sustaining this on a regular basis and tracking and tracing the rolls and any issues identified and rectified.’
ALT
Ade Morton, sales director at ALT, believes that ‘the anilox roller or anilox sleeve is the very heart of the flexographic printing process. It is therefore of great importance that the printer has some method of looking at a high-powered level at the condition of the anilox roller or anilox sleeve.’
He says that implementing a ‘track and trace’ auditing system will allow printers to identify five key issues: contamination, surface damage, score lines, chipping and staining. ‘The above issues will all cause print defects, often resulting in re-work or product rejection, as we are working with a very controlled surface and in micron depths any imperfections can be seen clearly, a very small slight surface scuff could damage hundreds of cells.’
As a result, he says, ‘anilox rollers should be checked over after every print run, this is easily done at the cleaning stage as the operator is in close contact and visually observing the anilox and looking for any changes.’
In terms of a full audit, Mr Morton suggests that this needs to be done at least annually. He explains, ‘A yearly audit of the anilox inventory is essential. The audit can be done in many ways, on press with controlled pulls on a controlled ink and controlled flexo head set up and colour readings, with high powered inspection equipment, or with a draw down system.
‘New developments in engraving technology are helping us to reduce the impacts of some of the issues we see, here at ALT we are seeing more of our elongated technology being utilised as this can help with cells evacuating ink and coating better and running cleaner, this can help in reducing the cleaning cycles. The elongated technology can help to reduce scoring issues as foreign particles are allowed to move freer under the doctor blade and in the cell, thus reducing the possibility of particles lodging behind the doctor blade and scoring the anilox roll.
‘Whatever method of anilox inventory control is selected, the key is sustaining this on a regular basis and tracking and tracing the rolls and any issues identified and rectified.’