For colour consistency and job repeatability, delivering and metering ink to the anilox roller needs to be done correctly. If it is, the system can realise the true volume of the anilox roller, by Michal Lodej.
After years of being relegated to jobs with low graphics requirements, flexography now rivals other printing methods for quality and efficiency, due in part to advances in the ink delivery process. Specifically, doctor blade chamber systems allow for better control over ink film thickness, colour consistency, ink consumption, cleaning costs and press run time.
A chambered doctor blade system uses two doctor blades along with an enclosed ink chamber to dispense the ink to the anilox roller. The reverse angle blade acts as the metering blade and wipes excess ink from the anilox roll, and the trailing blade acts as a capture or containment blade and holds the ink within the chamber. Foam, rubber or felt gaskets seal both ends of the chamber and keep ink from leaking out.
The enclosed chamber design provides protection from evaporation of solvents or amines from the ink, depending on whether the ink is solvent or water-based, so a printer can maintain ink viscosity. Also, the ink is sheltered from dust, and slinging and skimming on the surrounding area are minimised. Better control over ink usage means lower ink consumption by as much as 15% per year. The system holds less ink than open pans, so there is less leftover ink at the end of a press run, and this ink can be removed and stored for future use.
Doctor blade chambers also allow for a more efficient and eco-friendly cleaning process than open ink systems. A smaller amount of cleaning solution and water are needed, so cleaning solution and water usage are reduced along with disposal costs. Colour changes are quick, speeding up changeover and setup time on a run.
The two camps
Chambers can be broken down into two main categories, which have subtle differences to complement their intended market.
Flexible packaging chambers generally have an asymmetric profile and a lower volume of ink. The asymmetric profile massively reduces the impact of back doctoring on modern high-speed machines. This reduced angle on the retaining blade allows the ink to re-enter the chamber rather than metering it off, creating back doctoring. Flexible packaging also has an issue with ghosting, especially with the advent of faster inks and minimal use of retardants.
Absolute produces a range of flexibles chambers that have a third blade which often resolve this substantial issue.
Chambers intended for the corrugated market generally incorporate a much larger cavity with a correspondingly higher volume of ink to cater for a wider print surface with a significantly increased laydown volume. The largest absolute have produced was over 6500mm.
Obviously, a chamber should have the correct metering angle which is critical to give you the true volume of the anilox roller. To achieve this the supplier should have a wide range of chamber profiles to suit different sizes of anilox rolls. Typically 12 different profiles for a full range of flexibles chambers alone. It is clear, a chamber used for a 300mm diameter anilox would not be suitable for one of 150mm, the angle will be way off optimal. As the chamber is a fixed profile then the chamber itself would have to be changed.
Applying the screw
Will Whiteside, UK/Ireland technical support at Absolute explained, ‘Chambers should be operator friendly; this means having a simple but consistent blade clamping system, avoiding chambers that involve manual tightening with screws. Manual tightening of each screw will cause waves and creases along the doctor blade surface, which will affect the optimal metering angle of 30-35 degrees and ink will leak as the blade contact with the anilox is not uniform. This will also have a detrimental effect on blade life, reducing productivity. Having an easy clamping system also improves the health and safety considerations, you are more likely to shear an allen bolt or screw head on a manual tightening system and cut yourself on a blade. Selecting a tool free clamp system on your new chamber ensures the clamps and blade are easily and safely removed and changed.
‘Reliability and durability are key features on any chamber, after all they should last as long as the machine. Complicated blade clamping systems with lots of components will inevitably get clogged up with ink, rendering them ineffective and needing significant maintenance before replacement. Material also affects durability. Aluminium extruded chambers will corrode and warp over time, again to the detriment of the metering angle. The industry now accepts that woven carbon fibre is the premium material, and that’s why Absolute offer a 15 year anti-corrosion and splinter guarantee on all of our units.’
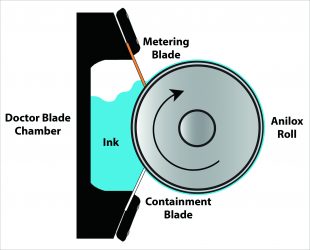
What goes on inside the chamber, stays in the chamber
A chamber is only as good as the mechanism used to load it on to the anilox roll. Putting a new chamber on to a crossbar or loading system that is worn or not working effectively will bring some results, but can represent a missed opportunity. Think about it, if one side of the loading system is loading at a higher pressure than the other, then you will get uneven blade wear and you may even be bending the blades on one side causing excessive wear on anilox, blade and seal. It is important that your supplier has experience in the whole ink circuit to appreciate whether this could be a problem with your upgrade specification.
Mr Whiteside concluded, ‘A good chamber should allow you to keep the metering angle consistent and the correct loading pressure will ensure a clean wipe and accurate metering of the anilox. This will ensure minimal downtime and stop any premature blade wear and additional costs associated. Whatever your criteria or budget, it’s always worthwhile speaking to the experienced market leaders first! This will give you a great base on which to make a logical and correct decision.’
Keep it light
Recently, chamber producers have incorporated innovative engineering concepts and next-generation materials to improve the equipment’s performance and usability. A good chamber must meet all health and safety lifting regulations. Utilising carbon fibre chambers keeps the chamber super lightweight making it easier to move up and down the machine, or fold back for blade changes. Lightweight chambers also run at lower pressures, meaning slower blade and seal wear and therefore extended periods between downtime, all adding to productivity gains.
New carbon fibre constructions are lightweight, strong, durable and temperature-stable, and they reduce press vibrations even on wide-format presses. Their surfaces are coated with resin to provide anti-static, corrosion resistant properties. Advanced clamping systems, like Tresu’s E-Line and P-Line Systems, replace screws with eccentric and pneumatic apparatuses, respectively, to make blade changes faster and easier for operators.
Early chamber systems were designed for use with steel blades. But, to address the increasing demand in the industry for plastic doctor blades, Tresu worked closely with doctor blade manufacturer Flexo Concepts to develop the exclusive new Series XL Blade Holder. The interchangeable quick-change clamp apparatus can accept slightly thicker TruPoint plastic doctor blades, giving printers access to a much wider variety of blade options. Those who prefer plastic blades over steel – whether to improve safety, extend blade life or solve press problems like UV ink spitting – have the flexibility to use plastic or switch back and forth between materials based on job requirements.
When selecting a doctor blade chamber, there are several factors to consider in order to maximize the return on investment. The doctor blade chamber and its loading system should prevent blade misalignment and ensure even contact across the face of the anilox roll. It is also important to make sure that the system allows operators to adjust pressure between the doctor blade and anilox roll. Minimum pressure, particularly when using TruPoint blades, is important to optimise print quality, prolong blade life and preserve anilox integrity.
Today’s flexo printers are able to produce attractive packaging in a cost-effective way thanks in part to the benefits provided by doctor blade chambers. These enclosed systems contribute to high print quality and bring considerable efficiency and cost savings to the pressroom. Along with cutting-edge press, ink, substrate and doctor blade innovations, advances in chamber technology have further improved the ink delivery process, making flexography a viable option for today’s most demanding print applications.