The most technical part of the entire flexo process is the production of screens, pulling knowhow from the worlds of physics, chemistry and engineering, to create structures invisible to the naked eye. By Michal Lodej
With the evolution of the flexo printing process, platemaking has moved from film-to-plate to direct-to-plate, but this change brought an unintended consequence; dots became roundtopped rather than flat-topped due to the loss of the oxygen inhibiting film which is inherent only with film-toplate. Eventually plate technology providers solved the problems of oxygen exposure by effectively putting a film layer over the plate. Plate makers could again generate polymer plates with flat-top dots, and the screening of smaller halftone dots too became possible, allowing screening to become more sophisticated.
Each screen uses a slightly different dot size, shape, and spacing in each colour that ensures that they do not interfere with each other. The dot algorithm further interleaves the dots in one colour with the dots in another producing what is called a stochastic rosette. This eliminates screen angles and angle clashes, as well as moiré between the dots in the different colours.
Bellissima is a set of Digitally Modulated Screens (DMS) developed by Hamillroad explicitly for flexography. These screens are imaged at 4000dpi and provide a high level of image reproduction (greater than 300lpi equivalent). There are two primary DMS screens: a Standard screen with 300–400lpi resolution, and an eXtended screen of 350–450lpi resolution. The eXtended screen uses slightly smaller dots that are a little closer together, thereby enhancing fidelity, while the Standard screen has dots that are more robust.
The Standard screen uses dots designed for wide web printing and offers flexible packaging printers the ability to print at resolutions of 300–400lpi. Some printers may be concerned that the dots employed to produce such high fidelity may not be durable enough for use with longrun jobs. The root cause of durability problems is unstable dots on a plate, and not small dots per se. Unstable dots can break off the plate, or they fatten up on press, causing dirty or muddy looking print. Bellissima DMS plates are capable of extremely long runs by creating dots that are stable and durable.
Bellissima’s eXtended screen is helping flexo trade shops and converters win business from offset. A label printer, based in Germany, was producing offset labels for a large European pharmacy brand. The printer was struggling to cope with increasing costs, in part due to 800 metres of offset make-ready waste each time he went on press with a particular job. The printer discussed his concerns with its trade shop, who suggested using flexo with Bellissima DMS screen plates instead. The printer agreed, put the job on press, ran the job, and got to colour much more quickly, reducing his makeready waste down to 150 metres. The brand owner was more than happy and signed off on the labels. The label printer is now converting more of his offset work over to flexo with Bellissima, which is now his screening of choice.
One particular wide-web flexibles printer has reported using a single set of Bellissima plates, imaged on MacDermid ITP60 material, for a job that ran at 300m/min for 1.6 million linear metres. The print results from the first pull to the last remained stable, consistent, and repeatable.
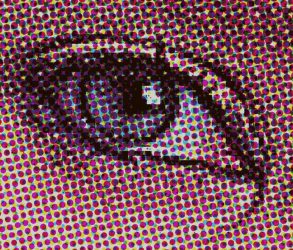
Conventional screening
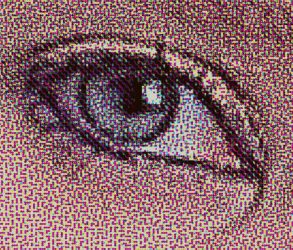
Bellissima’s Standard screening
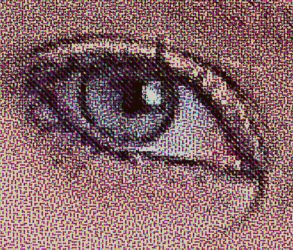
Bellissima’s eXtended screening
Mix and match
Using a combination of the Standard and eXtended screens, Bellissima is effective for fixed palette/extended gamut printing. Taking the CMY from the eXtended screen for CMY, and the CMY from the Standard screen for OGV and the K from either screen, printers can run seven-colour prints on narrow and wide-web easily.
Bellissima’s stochastic rosette stops interference between the dots in any of the colours and, therefore, no moiré. It also delivers flat tints that are as smooth and sharp tinted, and reverse tinted text.
The technology has helped make one of FGS’s clients’ fixed palette vision a reality. Flexographic Solutions S.L. (FGS) is a flexographic trade shop based in Barcelona, Spain. Specialising in the production and manufacture of photopolymers, ITR sleeves, and engraved elastomer plates, FGS has offered its pre-press services to printers of the flexible packaging market for more than 20 years.
One specific customer of FGS, a wide-web flexibles printer, was initially reluctant to print using more than four colours on its wide-web press and communicated its concerns to FGS regarding colour stability when printing with fixed palette inks. FGS discussed the benefits of Bellissima with the printer, who agreed to begin a test print. Joan Rodriguez Cosano, technical director at FGS, commented, ‘The print test helped our customer to realise the results quickly, and after the test, he transitioned to running fixed palette jobs on the press full-time.’
Using Bellissima, the client has reduced the time on press by an hour per job due to the elimination of press wash-ups, shorter makeready times, and reduced waste from misregistration issues. The printer has quantified this to be a 30% reduction in costs per job. This is excellent for the printer and FGS as it means that we can retain and grow the client.’ The printer is currently converting all its other printing presses to Bellissima DMS.
The Woodpecker Way
‘We all thought we knew about screening in flexo or dot-screens conventional (AM), stochastic (FM), hybrid (AM/FM) combinations, object based and even dynamically modulated varieties,’ said Doug Mawdsley, product manager – Xeikon pre-press, ‘These gave us great scope to reproduce tones in print getting towards photograph quality. We were just getting the hang of it and then someone comes along and puts another screen on top!’
Surface screens, or surface microstructures are not a particularly new phenomenon in flexo. Earlier photopolymer suffered an unflattering comparison in terms of solid-ink laydown against the molded rubber plates they were replacing. It was noticed that sometimes, the 90% screened area was actually printing a higher density (SID) than the full solid 100%. Thus the first surface screens were born, an extra screen of around 400lpi with a 90% tint was applied in solid areas to assist the ink-transfer. This was not well known and can hardly be described as successful.
The event of Flat-Top-Dot technology, reducing oxygen inhibition during main exposure by lamination, oxygen replacement (by gas), layers built into the plate or ‘out-running’ by fast and powerful LED exposures, made very effective high-frequency surface micro-structures possible.
These fine structures enable a noticeable increase in solid ink density, with a far smoother appearance and increased quality of ink laydown, fine details with reduced edge effects and cleaner dots with less bridging.
Mr Mawdsley added, ‘The ThermoFlexX approach to screening for tonal reproduction is very simple. We are laser system experts and don’t make workflow or RIP systems. So, ThermoFlexX imaging systems are totally open to facilitate the very best screening methods available. All industry resolutions, 2400, 2540, 4000, 4800 and 5080, and custom options, are supported. This ensures that the systems fit comfortably into any workflow and reproduce any
chosen screen, perfectly.’
Mr Mawdsley continued, ‘For the new variety of screen, surface micro-structures, a fresh approach was needed. Woodpecker SuS was developed to take advantage of ThermoFlexX higher resolution optics. If a client workflow produces files at 4000dpi with the common MCWSI pattern built in, then Woodpecker T01/Replay mode can reproduce these faithfully with the single pixels automatically detected in the file and boosted to a pre-defined laser power level to ensure sufficient UV light for good exposure. More interestingly, files of standard resolution, 2400 or 2540dpi, using 5080dpi optics for output, can output a finer (than MCWSI at 4000dpi) surface pattern at the imaging stage. In other words, standard legacy image files can be imaged onto digital flexo plates with greatly enhanced printing capabilities.’
Finally the Woodpecker Nano was developed. This operates with standard resolution image files, 2000, 2400 or 2540dpi but has the highest frequency pattern available with digital flexo (LAMs) plates. Higher resolution output optics are essential for this peck-per-pixel technique. The closer, perfectly symmetrical patterns can be applied to a variety of tone screens with less chance of interference than the lower frequency options.
Most RIPs now provide surface screening options. All competitive imager manufacturers have solutions or wish to develop them. ThermoFlexX, as part of Flint Group, has the advantage of close co-operation with Flint Group Flexographic to develop, provide and support full equipment and plate packages. ThermoFlexX imagers, Catena-E UV LED exposure and Flint Group nyloflex plates are vital parts of this comprehensive solution.
Intelligent flexo
Paul Bates, sales manager UK, Ireland & Global Accounts at Hybrid Software said, ‘The flexo market is always looking for the next big technology to help improve the print quality. The trend over recent years has been print at 4000dpi combined with a high definition modulated screening algorithm, which has solved many problems but also introduced instability on press and reduced platemaking imaging speeds, locking customers into one system.
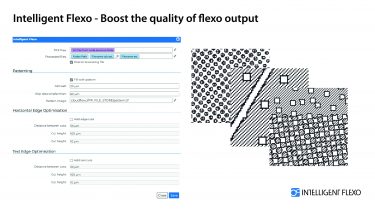
Intelligent Flexo brings new workflow functionality to Hybrid Software’s CLOUDFLOW
‘We worked with our RIP partner Global Graphics to developed Harlequin Cross Modulated (HXM) this is hybrid AM/FM screening for flexo that allows higher screen rulings than provided by AM screens alone, unlike other systems we have designed HXM to work with any output device and flexo plate manufacture. HXM screening combines the advantages of both AM and FM screening and is therefore able to limit the loss of small printed structures and detail at high line screen rulings by controlling the dot size in the highlight and shadow. It limits the smallest structure produced to be that which can reliably be printed on the target system. Once this point is reached within a given HXM screen, structures are removed completely rather than continuing to be reduced in size to create the required tonal range. Therefore, it does not disappear in the light areas or merge in the dark areas, which improves the print quality with smoother tones, flat tints and gradient transitions.
‘We have been thinking outside the box to bring to market a totally new concept, Intelligent Flexo’ Mr Bates continued, ‘Intelligent Flexo, brings new workflow functionality to Hybrid Software’s CLOUDFLOW, which can apply screening modifications intelligently to post-ripped files. Working on post-rip data we have more control and better tools to identify problem areas in the images that warrant intervention. The intention of Intelligent Flexo is to help overcome issues that are inherent with high speed flexographic printing processes which are consistent in an automated and repeatable process.’
Crystal clear
The latest 20.0 release of the Esko’s Print Control Wizard software provides new features, including enhanced test charts and a new platemaking wizard.
Released last year, Print Control Wizard was designed to improve the flexo plate making process and flexographic print quality via Crystal Screens. It offers a simplified, standardised approach to take several process parameters such as ink, printing press, substrate and anilox into consideration for screen and curve creation. It then outputs a set of Crystal Screens and dot gain compensation curves used for plate exposure on a CDI Crystal XPS.
‘Print Control Wizard was developed in response to industry calls to simplify the implementation of screens and dot gain curves, and we wanted to build on our immediate success of the wizardstyle user experience with additional functionality,’ said Robert Bruce, RIP & screening product manager, at Esko. ‘That’s why we’ve added integrated colour management tools and optimised the implementation process. For example, while global standards call for three press trials to define a flexo print condition, from optimisation with single screen testing, through characterisation with colour management and a fingerprint for dot gain, Print Control Wizard 20.0 users can now go straight to fingerprinting. This offers a significant reduction in time, cost and press downtime too.
‘Our goal was to provide flexographic pre-press experts with the tools to standardise and simplify screening and dot gain curve creation, enabling them to achieve the best quality results without additional steps and checks being added to the process,’ Mr Bruce finished, ‘After Print Control Wizard was honoured with a number of top industry awards, we have been working tirelessly to develop these new enhancements.’