The mantra of a modern day flexo printing operation is, ‘If you can measure it, you can control it’. Using digital cameras to inspect every label or pack as it is printed along the web is an essential part of measuring what you print. By Michal Lodej
Efficiency comes from making sure every action performed within a business contributes to a saleable product, as quickly as possible and at the highest possible quality. For a printer to be efficient, it will need to know that the press is doing, to achieve the graphics which have been ordered by the brand owner. If you get to the end of a run to find the colour is not right, the print is not in register or the print is covered with defects, then that is a lot of time and money down the drain.
Printing inspection systems are used in nearly every print process, although being one of the faster processes around, systems for flexo need to be able to operate on webs going at high speed.
Premonition
The systems in place need to know what they should be seeing on the web, with the use of a master file or proof, to compare to the printed product. However the more information the system can use before the run starts, the better. Some systems can integrate into a company’s management information systems (MIS) to get all the information it needs.
BST eltromat International recently collaborated with Hybrid Software for PDF-based pre-press-stage workflows and linkups to the MIS for quality assurance in narrow-web production processes. This cooperation has enabled the companies to considerably simplify and speed up set-up processes in label printing.
With the PDF option, machine operators can ensure that their printing systems produce perfect quality instantly.
Machine operators will no longer have to scan proofs and then compare them to the specifications from the pre-press stage. Trips to the scanner and back, and the time involved in that process step, are things of the past. Label producers are printing faster than ever, and reducing the amount of waste they generate at the same time. This is possible because the PDF files for print jobs that the pre-press stage creates using Packz from Hybrid Software contains all the relevant parameters, including the requirements for inspecting the jobs that need to be printed.
This also applies to repeat lengths, efficient use of the web, and defining the inspection zones. The pre-press stage is also able to define different inspection requirements for each zone, making them more or less stringent as necessary. For example, selected zones can be inspected in more detail than less critical zones. A highlight: All objects can now involve dynamic, variable data such as different barcodes or alphanumerical – even randomised – sequences. During the setup process, the actual print results are compared to the specifications in the PDF files right in the printing machines and corrected by the operators as required.
The main concerns of the QLink workflow from Nyquist Systems, a partner of BST, for the TubeScan product family are integration with customer ERP systems, expanded options with its new 4k high-resolution area scan camera, and the new Contour Light illumination option. This laterally directed light source can be used to make the outlines of transparent labels visible on paper or plastic carriers. The TubeScan range can be used for diffused standard background illumination, background illumination through the web, and UV illumination for security features. In addition to the new contour light,
it also features three other independent illumination sources that cover a number of different web monitoring and 100% inspection requirements.
On application
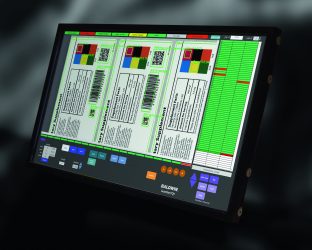
Baldwin’s Guardian PQV 100% Print Inspection provides print quality verification
Grafikontrol’s TQC-360 family includes different 100% inspection systems, each one dedicated to a specific application. Most recently, a new device was added to complete the most difficult part of the process; defect tracking through the production process and the defect removal from the printed rolls.
Lynex is a 100% print inspection system developed to assure total quality control during the printing process. The continuous inspection of the entire print repeat, with programmable sensitivities, allows the automatic detection of all print or substrate defects and a real time evaluation of the production. The immediate warning, when a flaw is detected, guarantees the elimination of defective material which optimises the process. The modular architecture, combined with powerful hardware and dedicated algorithms for image processing, makes the Lynex a flexible and easy to use instrument for inspection on gravure, flexo and offset presses. Lynex can operate as a standalone module in multiple processes, as a print or substrate inspection device, or in combination with the Matrix.
Lynex C/S is a 100% print inspection system for gravure and flexo dedicated to inspecting clear coating and varnishes. The custom-made design of the illuminators and special optics identifies defects for coating applications on printed or base substrates. In combination with Lynex it provides the total control on both sides of a printed web.
Matrix is a sampling video camera that operates as an independent system or in combination with the Lynex 100% print inspection. It is equipped with motorised zoom for the viewing of print details and can be supplied with a specific software for automatic defect detection, thus providing the operator with a more effective print control tool compared to a simple web viewer. A special add-on
on illuminator can be supplied as an option for the viewing of clear coatings or UV varnishes.
Progrex is the system that combines the functions of Matrix and Lynex for wide web presses running up to 800m/min. The combination of these two technologies forms a tool that helps the operator in every control phase. In addition to the 100% print inspection, Progrex provides the following features: Bar-code verification, ∆-Colour monitoring, PDF-Live master verification, and print elongation monitoring.
The cost of no inspection
The consequences of not having a 100% inspection process can be severe. Missing or broken text on a pharmaceutical label could be a matter of life and death. Inaccurate variable data on security print can result in massive costs and litigation. Even if you’re not printing in those highaccountability scenarios, everyone should consider the high cost of returns if you fail to ensure that no defects get into the hands of your customers. Think about the cost of customer rebates, or liability exposure, or labour and materials required to repeat a print run. Beyond that, what is the cost of losing a customer and their future business?
Lynex C/S is a 100% print inspection system for gravure and flexo dedicated to inspecting clear coating and varnishes. The custom-made design of the illuminators and special optics identifies defects for coating applications on printed or base substrates. In combination with Lynex it provides the total control on both sides of a printed web.
Matrix is a sampling video camera that operates as an independent system or in combination with the Lynex 100% print inspection. It is equipped with motorised zoom for the viewing of print details and can be supplied with a specific software for automatic defect detection, thus providing the operator with a more effective print control tool compared to a simple web viewer. A special add-
Baldwin Vision Systems’ global branding PR & communications manager, Craig Du Mez, said, ‘We have focused our research and development efforts on more efficient,
accurate, data-connected inspection workflows. We’ve developed new technologies that enable press managers to monitor changes as they happen, and make highly-informed decisions about print quality, defect management, and even operatorto-operator performance.
We’ve developed solutions that simultaneously collect data for multiple presses, jobs, and even across multiple plants to meet the challenges of increasingly sophisticated packaging techniques.’
The company has a portfolio of products within the inspection sector. Its Guardian PQV 100% Print Inspection provides complete print quality verification from pre-press through to production, reporting, and archiving. Printers and converters can eliminate every defect with a more efficient, accurate, data-connected workflow. Guardian PQV delivers advanced, automated, inline defect detection for the entire production process. This system is designed to perform for all printing applications including converting, label, packaging, sheet and web. Guardian PQV is also suitable for working within regulated industries including currency, banknote, security, and pharmaceutical.
Baldwin’s Guardian RTM (RealTime Monitoring) uses a central server to monitor, collect, and display real-time inspection data on a dashboard. RTM can simultaneously collect data for multiple presses, jobs, and across multiple plants.
The combination of Guardian PQV and RTM ties together how printers manage their processes, customers, and people. Users are able to identify any mechanical issues, process inefficiencies, and can tailor operator training to eliminate defects.
The Guardian OLP Offline Proofing & Inspection verifies that the files used for production match the customerapproved master file. By comparing any pre-press file or scanned press sample to the customer-approved original in a matter of seconds, advanced software automatically locates and highlights even the smallest of differences in print quality.