The absence of good cleaning practice for anilox rollers will lead to the reduction of the available cell volume and difficulties in transferring the correct amount of ink to the plate. This will result with inconsistent print quality, wasting both time and money. Michal Lodej reports.
Anyone using an anilox roller for printing or coating will realise the benefits of keeping the roller clean. Regular deep cleaning of the anilox is the key to quality and consistency. A clean anilox has to be seen as a quality tool. It ensures an even higher output on the press with less set-up time and reduced labour costs.
The cleaning of a ceramic laser engraved roller is a complex problem. Screen counts are becoming finer and finer, inks and coatings are becoming more complex. As a result, the quality of printing in flexo has increased dramatically over the years and the need to deep clean the roller has become a greater challenge.
As well as coping with different types of inks and coatings there are varying screen sizes and cell depths. Whilst hard wearing, anilox rollers are also delicate and cell walls can be damaged during a cleaning process if the correct process is not used.
The art of flexo
Steve Turner, managing director at Print Tech Solutions said, ‘We encourage customers to think of the anilox roller as an artist’s paint brush – the roller is used to deposit ink onto the printing plate, just as a brush is used to put paint onto a canvas. The principles are the same; just as an artist would never use a dirty or damaged paint brush, flexo printers cannot hope to achieve high quality, consistent print if their anilox rollers are not maintained and regularly cleaned.’
If the cells become contaminated with ink residue, it will have a direct impact on the amount of ink deposited onto the printing plate. In turn, this will reduce the density of the printed colour, forcing the printer to boost colour strength of the ink to compensate. However, this compounds the problem as high viscosity inks tend to dry significantly faster and become even harder to clean from within the microscopic anilox cells. Ink colour pigment is also an expensive part of ink formulation; therefore the extra costs involved in compensating for a dirty anilox roller can be significant.
This problem will usually affect printers using water-based inks, as they are formulated to withstand tough environments and will dry readily both on the surface and within the cells of the anilox roller, causing contamination and reduced cell volumes.
Mr Turner continued, ‘During our site visits we often find customers using unsuitable generic cleaning chemicals to tackle the problem, which can cause immediate or long term damage to anilox rollers, ink chambers, rubber rollers, pumps and pipes. Our advice to customers is always to be proactive in maintaining the anilox’s condition.’
For customers who are unable to clean rollers off press, the company’s smart range offers cleaning solutions which are formulated specifically for flexo press cleaning. In particular, smart Aquasol is a daily cleaner designed to remove water- and UV-based inks and coatings from all areas of the printing process. It is suitable for use on anilox rollers, rubber rollers, polymer plates, ink pumps and doctor blade chambers.
Within the corrugated market, large anilox roller are subjected to tough conditions and daily long runs involving water-based inks which can cause deep contamination of anilox cells. Print Tech Solutions has worked with customers on a developmental project to combat this issue, which led to the launch of smart Revive, which has seen huge improvements in cell volumes after cleaning. smart Revive is formulated specifically for periodic cleaning of anilox rollers and effectively removes plugged contamination within anilox cells.
Mr Turner concluded, ‘Whilst cleaning techniques and products play a key role in colour management, they don’t fix the problem alone. It’s vital that printers, supervisors and managers at all levels fully appreciate the importance of allocating time to anilox care. Our company has built its ethos on supporting the use of our products with onsite training and regular service visits, providing our customers with valuable support and an early warning system for anilox condition issues.’
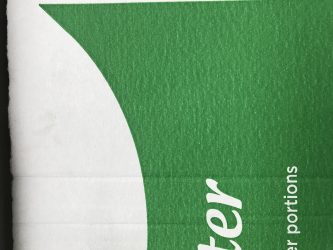
A print sample before cleaning
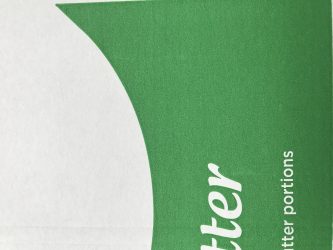
A print sample after cleaning
Making waves
There are many methods of cleaning the anilox; all have certain merits, and one such method is the use of ultrasonic waves, within a cleaning liquid.
Early use of this method caused problems with damaging the anilox, the danger lies in the creation of hot spots and dead spots within the cleaning liquid – known and nodes and anti-nodes. These occur when sound waves generated at the transducers, travel to the top of the liquid and, on returning, collide with the next wave. This creates a hot spot of intense cavitation, below and above which there is formed an area of less cavitation – a dead spot. These hot spots are potentially harmful to ceramic anilox roller cells.
Safe ultrasonic cleaning relates to the need for the centre frequency to remain constant during changes in transducer temperature or the effect of a heavy roller being placed in the tank. Caresonic has ensured this stability by designing and installing an auto tracking circuit, which compensates for external changes and maintains the centre frequency.
This auto-tracking circuit also prevents the transducer elements hitting their resonance and drawing an unequal amount of power – possibly leading to overdrive. In such cases, the power drawn by an individual device could double, which would further add to damage of the cell walls of the roller.
It is also essential to ensure that the transducers do not run hot internally as this could lead to uneven distribution and components failure. Again, Caresonic has solved this potential hazard by using high quality bronze conductors, purpose-built to a registered design, and employs special assembly methods, which prevent internal heating problems.
Print Tech’s Mr Turner added, ‘For customers who can take anilox rollers quickly and easily out of the machine, the fastest and most efficient cleaning method is ultrasonic cleaning. This method uses a combination of finely tuned ultrasonic soundwaves, specific cleaning solutions and heat to gently remove ink deposits from within anilox cells.’
Alphasonics has been producing anilox rollers cleaning systems since 1992 and has been able to develop its equipment in line with screen count rises, and according to the company if a 3000lpi anilox was launched tomorrow, a system would be available to clean it the day after.
It is becoming increasingly clear that the anilox should not just be kept clean, but it should be controlled. This is achieved by using a cleaning system that has the ability to safely render the roller 100% clean every time, to deliver a consistent base line from which to work.
Alphasonics’s technology is also being used in other sectors, such as healthcare, where its equipment is cleaning surgical instruments. David Jones, managing director, said, ‘Within the development of the healthcare device, we had to come up with a validation system that would accurately show exactly what is going on within the tank fluid on a weekly basis.
The resulting device is called CVD (cavitation validation device) and what this equipment actually showed us even surprised our engineers. We knew our kit was good, but now we can prove it conclusively.
‘Ultrasonics when applied into fluid is very patchy, with areas of high activity as well as areas of low or even no activity and it is this disparity that has the potential to damage an anilox roller. However, there are ways of greatly reducing this ‘spread’ to a point where it is incredibly small. The one thing that our healthcare project showed us is that the ‘hot’ and ‘cold’ spots can never be completely eradicated, but can be rendered so tiny that they cease to be an issue, thus making the system completely safe for hourly, daily, or weekly cleaning of even the highest screen counts because the sound is so evenly applied.’
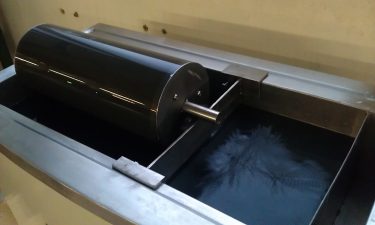
To use ultrasonic waves, the anilox is submersed into a cleaning fluid
Laser Point
Laser technology can reach all the geometries and achieves the maximum recovery of the volume of the cells. However as a technology it can be dangerous, and if incorrectly used it can damage the surface of the anilox. The right formulation of power, frequency, speed, focus and time to perform selective ablation to remove ink without damaging the surface, must be achieved.
Sitexco Systems incorporate all the necessary security features that make laser cleaning the most effective and safe for the operator, the anilox and the environment. They are completely automated and easy to use, intuitive and versatile. According to the company, a volume recovery in the cells of almost 100%, even in clear colours, are being achieved with both solvent and water-based inks. In more complex inks – UV, varnishes, lacquers – the results are more variable and, perhaps, less spectacular, although they greatly improve the quality obtained with other methods. TEG Technologies’ R&D department is achieving significant advances in these fields and improvements for short-term projects.
Flexo Wash’s area sales manager, Mette Laursen, agreed that prevention is better than cure, ‘The best thing is to be proactive from the beginning. Make sure that your aniloxes are properly clean from day one, and clean them after each job, and before storage. Never leave them standing around, because ink becomes more difficult to remove from the fine cells, and the longer the ink (or coating) dries in the cells, the more difficult the cleaning process becomes, and the more important a strict cleaning
method becomes. Pads, abrasive cleaners and brushes are losing their effectiveness in today’s deeper and smaller cells, and can also cause damage to the expensive roller.’ Flexo Wash supplies two ways of cleaning aniloxes: the first is cleaning with liquid and high-pressure water; and the second is the fast-emerging laser technology. Both give a good cleaning result and will reduce
downtime and expense from printing with dirty aniloxes. The company’s new Laser Washer was launched at Labelexpo Americas 2018. Ryan Potter, vice president of sales for Flexo Wash, USA, stated, ‘Our customers are excited to finally have an open and truly comparative conversation about the pros and cons of each technology. Flexo Wash provides the ‘flexobility’ for converters and printers to choose which system works best for them.’
Chemical reactions
Another aspect to consider is the types of chemical to be used in the cleaning process. According to the anilox manufacturer Harper Corporation of America, when selecting the cleaner and cleaning method the relevant environmental protection agency guidelines must be followed. All chemical cleaner SDS (safety data sheets) must be reviewed and maintained The company has even created a complete Cross Reference Chemical Cleaning Guide with recommendations on the correct chemical cleaner for the different press components. Methods covered in the cross reference guide are: manual/hand cleaning, ultrasonic, soak tanks, and auto-wash systems.
The guide states that it is important select a cleaner that has been specially formulated to remove the ink, coating or adhesive being applied without causing damage to the anilox cells or anilox base material. Proper mixing ratios for cleaners to be mixed with water are extremely important to clean effectively and not cause damage. Ratios are typically listed with water as the first number and the chemical as the second number. In general the best safety practice is to add chemical to water, not water to the chemical. It says, ‘We recommend testing to ensure the correct ratios are used and to determine the effectiveness of the cleaner. Remember the most important part of chemical cleaning is rinsing and drying. Rinsing the roller using water or a 50/50 mix of isopropyl alcohol/ water will remove any cleaner that may be left. This reduces the possibility of corrosion occurring which can cause damage to the ceramic and base materials. During the drying stages a lint free rag or cloth needs to be used to push the cleaner residue to one side, rotating the roll not to cause streaking or water spots.’
The best way to make sure anilox cells are clean is to use a microscope to visually see the cells at a magnified level. Handheld white light microscopes can show the difference between clean, plugged (dirty) and damaged anilox cells. Microscope measurement systems that use interferometric technology are the best method for reviewing cleaning effectiveness and verifying the current cell volume condition.